The past couple of days pouring rain has forced me to shift to indoor activities (like taxes, scholarship essays, and catching up on emails that have piled up over the past two weeks). So I've had a chance to reflect on what I learned from our week-long tiny house build. I figure by sharing my lessons-learned I might spare someone else a bit of head scratching and perhaps enable other folks to avoid the mistakes we made. (For a full slideshow of construction details, click here.)

First, building a small house that can withstand earthquake conditions requires some different considerations than traditional construction. We secured the frame to the trailer with HTT tension ties and 10 inch bolts and we'll be attaching the roof with hurricane clips, so the structure is solid. But it was tricky finding the balance between building sturdy and building light. The two aren't mutually exclusive, but to have both one must plan strategically. I certainly don't think we've maxed out the trailer's hauling capacity, but we ended up using more studs than we would have needed if we'd planned so that our sheet goods, studs, and rough openings all lined up better. I have a much better understanding of how sheer panels, tension ties, and framing work now and I'm sure I could develop a better plan now than I could have two weeks ago. I wish I'd spent a little time between the day we picked up the trailer and the day we started building to puzzle through some of the connections in advance.

I've come to really appreciate the design-build process for its iterative aspects. One idea influences another, which affects another, which informs another. Over the past couple of months Jane and I had developed a general layout and we had salvaged quite a few materials, but we hadn't developed detailed plans. Every time I attempted more complicated drawings or Sketch Up models I was dissuaded either by questions I didn't know the answers to (like how we were going to attach the walls to the short ends of the trailer) or by reminders that whatever we thought the plan was, it would change once builder friends came on the scene. We deferred to their experience and the house emerged as the product of collective wisdom and effort. It's both similar to and different from what I imagined it would be. The layout has shifted a bit, the envelope systems have evolved, and the roofline gives the house a whole different character than I anticipated.

Despite a decade volunteering with Habitat for Humanity and two spring breaks of home restoration in New Orleans, I realized that I didn't know many of the details about how a house goes together. My only framing experience was building my chicken coop and solar trellis with my friends Jon and Phil, so my vocabulary expanded this week as I learned to name roof framing elements like outrigging, rakes, and gussets. I also became much more comfortable using a circular saw, jig saw, sawzall, and staple gun, though I'm still a little shy of the table saw. I learned that plywood is supposed to be oriented with the long dimension perpendicular rather than parallel to the joists and that OSB isn't necessarily a good substitute for plywood if there's rain in the forecast (if, for instance, you live in west of the Cascades!) Figuring out how to get the fenders into the wall system and close the space to the outside was a mental puzzle and I'm glad we came up with a good solution. I decided that for future tiny houses it would be great to have the fenders be structurally sound.

I also learned the hard way that it's worth taking time to do additional research and planning if using an unfamiliar product. The bubble wrap we were so excited about for its reflective heating properties caused a moisture problem in our floors. When we pulled up part of the floor to start the plumbing we found that the fiberglass insulation was damp. It seems that since we sealed the bottom of the floor system with plastic then stapled the bubble wrap across the top of the joists we created a waterproof envelope. This would have been great if everything inside it was moisture free. The trouble was that the joists we were using were made from green (wet) wood so as the house sat in the sun for four days the wood released its moisture. Since there was no way for the moisture to escape it settled into the insulation where it could cause mold or rot. When we discovered the problem I contacted a company that sells the material to troubleshoot. I was informed that we shouldn't have closed up the floors till the joists had dried out. If we couldn't wait for the wood to dry, we should not have stapled the bubble wrap over the joists; the moisture could have escaped the system if we hadn't sealed it in completely. We had originally planned to run the bubble wrap inside the bays and to not lap it over the joists, but once we started stapling the bubble wrap we found it was easy to go over the joists. I didn't take the time to think through why that might be a bad idea. Now we'll have to pry up the floors we screwed and glued down so that we can remove the insulation and bubble wrap and then re-insulate. With this reminder of building science basics, I think we could use the bubble wrap effectively if we installed it properly, but I don't blame Jane a bit for deciding to take it out of the envelope completely. Removing it will impact the insulation systems for our walls and ceiling since we had planned to use it throughout the envelope. At least we were also reminded that the plywood ought to have run the opposite direction so we'll fix that while we're at it and feel very productive for addressing two concerns in one fail swoop!
A few final thoughts:
It would have been a good idea to have our supplies delivered a day early and to check the delivery for accuracy. There was something wrong with almost everything ordered. (Working with a smaller company likely would have helped!)
Double-checking that the windows all fit into their rough openings properly before putting up the sheathing would have been a good step. We skipped it and had to do a couple tweeks later.
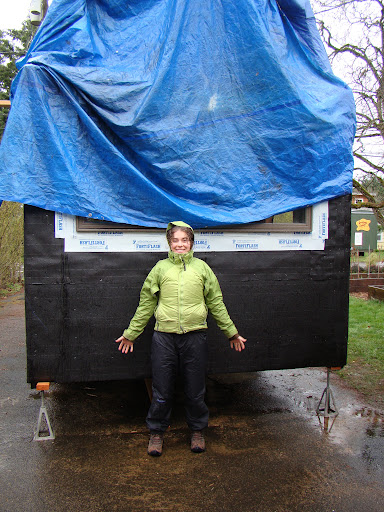
I'm thoroughly impressed with the ability of people who have been building longer than me to think through the multiple layers of a structure - planning ahead to the surfaces on either side and how they will all come together. I hope to continue honing my spatial comprehension the more I design and build.
It's great to be optimistic about the weather forecast and to be willing to work through some unpleasantries. But it's also important to establish a rainy day plan so that all your hard work isn't compromised by inclement weather.
You know you're ready for a break from building when you start cracking jokes about how you're ex-sided that the exterior siding is almost finished. Get it excited, ex-sided, exterior siding. Er. Um. Yes, I can see now that it wasn't very funny. See? Time for a break!
Building the shell of a tiny house on wheels was an awesome way to spend my spring break. There will still be lots of chances to contribute over the next few weeks, so if you'd like to help out, just let me know!